BLOG
Vacuum forming industry technology
August 20,2021
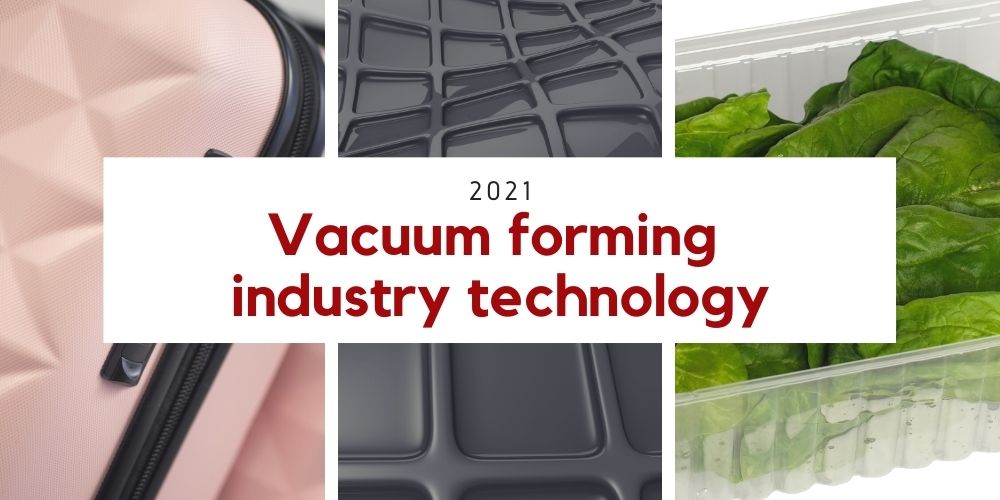
The all-weather vacuum forming car mat is currently the most eye-catching car mat product on the market, because of its special full-enclosed design, which perfectly fits the shape of the car floor, and is not only resistant to dirt and easy to clean.
It can also prevent spilled drinks from leaking, and protect the original carpet in all directions. Singform Enterprise has also recently begun to design and manufacture vacuum-formed car mats for well-known car manufacturers.
We have professional R&D personnel using 3D scanning instruments to build models. The experienced production line handles everything from raw materials to finished products, and then undergoes rigorous quality control inspections. Just to make the best car mat products.
At this time, the plastic can be covered on the mold, and then the interior can be vacuumed, so that the plastic can tightly fit the mold, thereby making the shape it should have.
When the product shape is formed, the production progress is almost complete. According to different plastic material specifications, different cooling times and trimming methods are formulated. It can be buckled and locked on the interior carpet, and it can also be drilled and cut.
According to the product specifications you want to make, such as thickness, color, transparency, abrasion resistance and other physical properties, determine the plastic raw materials. The commonly used materials on the surface are PVC, PP, HIPS, ABS, PET, PC, PE and acrylic Such as thermoplastic plastics.
Singform’s vacuum forming car mat material uses TPE material, which has excellent thermoplasticity, and has excellent physical properties such as wear resistance and weather resistance. TPE itself is also environmentally friendly, non-toxic and recyclable, so we can recycle the remaining materials in the production process.
If you want to make products with fine details, the vacuum forming process may not fully show the details of the product. Therefore, containers, packaging, auto parts, luggage and other products with less complicated details can be made by vacuum forming.
The technology of vacuum forming is actually not complicated. Some people even use ovens, wooden boxes, 3D printers, and vacuum cleaners to create DIY-type vacuum forming machines.
Industrial vacuum forming machines range from the production of large rear-car mats to small transparent container boxes, and their relatively easy entry barriers have also led many small factories to gradually introduce them to meet their small-scale and customized needs.
It can also prevent spilled drinks from leaking, and protect the original carpet in all directions. Singform Enterprise has also recently begun to design and manufacture vacuum-formed car mats for well-known car manufacturers.
We have professional R&D personnel using 3D scanning instruments to build models. The experienced production line handles everything from raw materials to finished products, and then undergoes rigorous quality control inspections. Just to make the best car mat products.
Vacuum forming process
Production method
Vacuum molding is the most popular technology for shaping plastic raw materials. First, a piece of thermoplastic plastic raw material is uniformly heated. The details such as thickness and size depend on the product mold you want to make, and when it reaches the optimal molding temperature after adjustment , The plastic sheet will become flexible.At this time, the plastic can be covered on the mold, and then the interior can be vacuumed, so that the plastic can tightly fit the mold, thereby making the shape it should have.
When the product shape is formed, the production progress is almost complete. According to different plastic material specifications, different cooling times and trimming methods are formulated. It can be buckled and locked on the interior carpet, and it can also be drilled and cut.
Applicable raw materials
According to the product specifications you want to make, such as thickness, color, transparency, abrasion resistance and other physical properties, determine the plastic raw materials. The commonly used materials on the surface are PVC, PP, HIPS, ABS, PET, PC, PE and acrylic Such as thermoplastic plastics.Singform’s vacuum forming car mat material uses TPE material, which has excellent thermoplasticity, and has excellent physical properties such as wear resistance and weather resistance. TPE itself is also environmentally friendly, non-toxic and recyclable, so we can recycle the remaining materials in the production process.
Advantages of vacuum forming
- The production time is shorter than the traditional injection time, which can effectively and economically save production resources and reduce fixed costs.
- The mold material is relatively flexible, such as wood and aluminum, and even some small businesses use 3D printers to make molds to meet low-volume production and save money and time in making traditional metal molds.
- Products that require sterility are also usually made by vacuum forming methods, such as food containers or medical materials, which can be made with non-toxic and compliant plastic materials.
Disadvantages of vacuum forming
If you want to make products with fine details, the vacuum forming process may not fully show the details of the product. Therefore, containers, packaging, auto parts, luggage and other products with less complicated details can be made by vacuum forming.
Conclusion
The technology of vacuum forming is actually not complicated. Some people even use ovens, wooden boxes, 3D printers, and vacuum cleaners to create DIY-type vacuum forming machines.Industrial vacuum forming machines range from the production of large rear-car mats to small transparent container boxes, and their relatively easy entry barriers have also led many small factories to gradually introduce them to meet their small-scale and customized needs.
► 想看更多產品 More Product【Click me】
► 立即洽詢 Inquire now【Click me】
► 阿里巴巴 Alibaba【Click me】